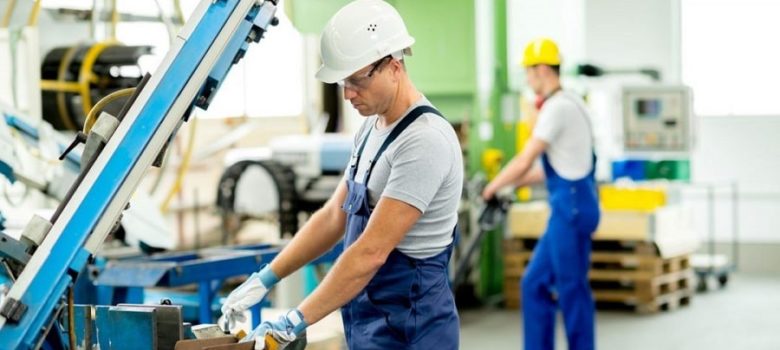
- Feb. 21
- Richard Parker
Should You Employ a Preventative Maintenance Strategy in Your Business?
A common approach used by many enterprises, firms, and organizations to schedule certain maintenance chores that allow assets, machinery, and other equipment to remain in good, operating condition is preventive maintenance. Tasks are typically scheduled based on the amount of time or equipment required.
In the case of a machine, lubrication may be required every 1000 hours of operation, whereas another asset may require an inspection or change out on a yearly basis. Maintenance checklists are frequently an important component of a well-designed preventative maintenance program.
In the end, the key advantages of preventive maintenance boil down to dependability and efficiency. As long as you keep each asset in good working order, it will be less likely to break down, and you will have less downtime over the asset’s useful life.
Implementing a Preventative Maintenance Strategy
What Are Your Most Important Assets?
Preventive maintenance plans should be implemented only once you have a clear understanding of which assets and processes would reap the most benefits from them. This is possibly due to the fact that businesses are concentrating on preventative maintenance actions that do not avert breakdown. In order to begin, it is necessary to identify vital assets that are susceptible to breaking down, and that can be avoided with a well-designed preventive maintenance program. By itself, simply inspecting every piece of equipment and carrying out routine maintenance chores will not always increase dependability or performance.
Schedule the Tasks Efficiently
In order to successfully implement a preventative maintenance program, you must first establish effective work patterns for your maintenance personnel. Your entire maintenance department will run more smoothly and efficiently if you can reduce the amount of time personnel spend commuting from one service project to the next. Additionally, you should schedule maintenance operations for times when production lines are organically down, rather than disrupting operations, to save time and money.
Incorporate Recurring Tasks Into Daily Operations
Once you have set a maintenance schedule, make sure to include frequent inspections before components or parts are likely to fail. This will help you avoid costly repairs later on. In this approach, you will be able to identify and resolve any possible issues before they become a problem and cause downtime. Never forget to pay attention to your operators and to document all duties, repairs, and labour accomplished so that you will have an accurate record to refer to in the future. It might be something as simple as cleaning – if you find the easiest way to clean pistons, it will become a natural part of your operational routine.
What Are the Advantages of a Preventative Maintenance Strategy?
Generates Savings by Reducing Downtime
Preventive maintenance programs can provide numerous benefits to a facility or corporation if they are properly developed and maintained. One of the most significant advantages is the improvement in overall equipment and system reliability, which allows assets and production lines to continue to operate without interruption. Reduced downtime or the elimination of emergency production line breakdowns can often result in significant cost savings for businesses.
Reducing the Number of Emergency Maintenance Work Orders
In addition, the use of preventative maintenance plans can help to reduce the frequency of unexpected breakdowns and emergency repair calls. Purchasing, shipping, and managing parts on overnight or urgent basis, which can be expensive over time, can be reduced as a result of this practice.
Preventive maintenance procedures that are implemented on a long-term basis can help to extend the total life of your equipment while also increasing its resell value. And, perhaps most crucially, you should see an improvement in overall efficiency as well as improved compliance with safety and health standards.
What Are the Most Common Errors With a Preventative Maintenance Strategy?
Setting Instructions That Are Not Clear
It can be difficult to manage preventive maintenance programs effectively, and many firms make the following frequent mistakes that can be costly in terms of both time and money. One of the most prevalent blunders is to provide directions that are imprecise and ambiguous. Make sure to provide particular measurements and tasks to be completed in your step-by-step instructions as well. Keep in mind that vague instructions can imply quite different things to different people. It is possible for maintenance professionals to mark a preventive maintenance activity as done without actually completing the work if the instructions are unclear. Instead, be clear with your directions.
Not Having a Reasonable Timeline
Although having a brief window of opportunity within which preventive maintenance chores should be completed is a good concept, it is crucial to remember that conducting preventive maintenance duties too early or too late can both cause difficulties. An organization can waste valuable labour and financial resources if a piece of equipment is checked or maintained unnecessarily. The majority of the time, routine maintenance operations that are performed too frequently do nothing to avoid failure and are therefore a waste of time and resources.
Not Prioritizing Correctly
Prior to starting a preventive maintenance program, it is critical to identify and prioritize the assets and activities that have the greatest potential for preventing system failure. Preventative maintenance plans should be tied to specific pieces of equipment that are critical to the operation of your production lines or the safety of your personnel. This will ensure that you get the greatest benefit from your preventive maintenance program.
Not Keeping up to Date Records
The most important thing to remember is to keep track of your preventive maintenance program so that you can make improvements and identify problems as they arise. A computerized maintenance management system can assist you in accomplishing this goal by offering extensive analysis and data that can be used to assist your management team in making more informed business decisions.
Not Making Sure You Have Everything You Need to Do the Maintenance Tasks
It is critical to have a well-stocked maintenance inventory on hand so that your maintenance staff have access to all of the tools, testing equipment, and other resources they need to complete their jobs promptly and efficiently. The frustration of starting a service request only to learn that you are missing critical tools is compounded by the fact that it is extremely inefficient.
Conclusion
Overall, a preventative maintenance program can be an effective tool to assist a company in reducing malfunctions, minimizing downtime, increasing efficiency, and increasing the lifespan of its equipment. However, like with any program, it is critical to understand the types of situations and the types of equipment that can benefit the most from a well-designed preventive maintenance program in order to implement one.
Make a list of the vital assets that are essential to the successful running of your organization on a daily basis, as well as those that are essential to employee safety and environmental compliance. Identifying possible failure reasons for those pieces of equipment will also be necessary so that a preventative maintenance program can be developed and implemented to improve the equipment’s overall dependability.
Make sure that you have all of the necessary tools, processes, and people in place to ensure that the program is successfully executed after the foundation has been laid. To ensure the success of a preventative maintenance program, clear and detailed instructions, as well as technician training, will be required. Finally, make sure you have a mechanism to keep track of all of your tasks, checklists, and previous history on an ongoing basis. The management team will have a valuable resource if high-quality data is captured throughout the process. This data will be used to monitor essential equipment performance and make more informed business decisions in the future.